Toyota Motor Corporation used the hl-3dw 3D scanner to obtain the 3D data of the pickup truck carriage for reverse design, and mass produced the pickup truck carriage with a size of 2*2 meters.
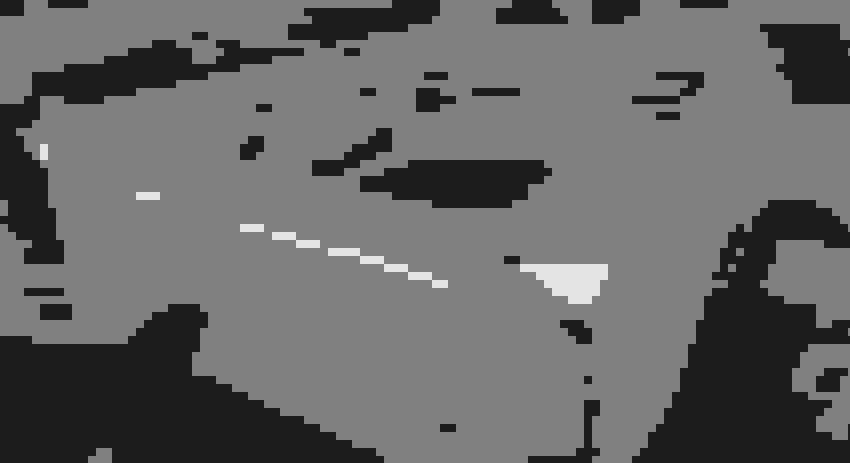
Practical problem
1. It is necessary to carry out rapid three-dimensional measurement and obtain three-dimensional digital model for pickup truck carriage, but there are many curved surfaces of the whole vehicle, which are also complex. In addition to improving the measurement efficiency and greatly shortening the measurement time, the measurement accuracy should also be well controlled, and the global measurement accuracy should be controlled within 0.1mm.
2. For the measurement efficiency proposed by the automobile company, the traditional gantry CMM not only costs a lot of equipment, but also can only obtain part of the data of the pickup truck. It is impossible to measure the curved surface and the parts with large slope, resulting in incomplete data and the inability to carry out the secondary design of the pickup truck.
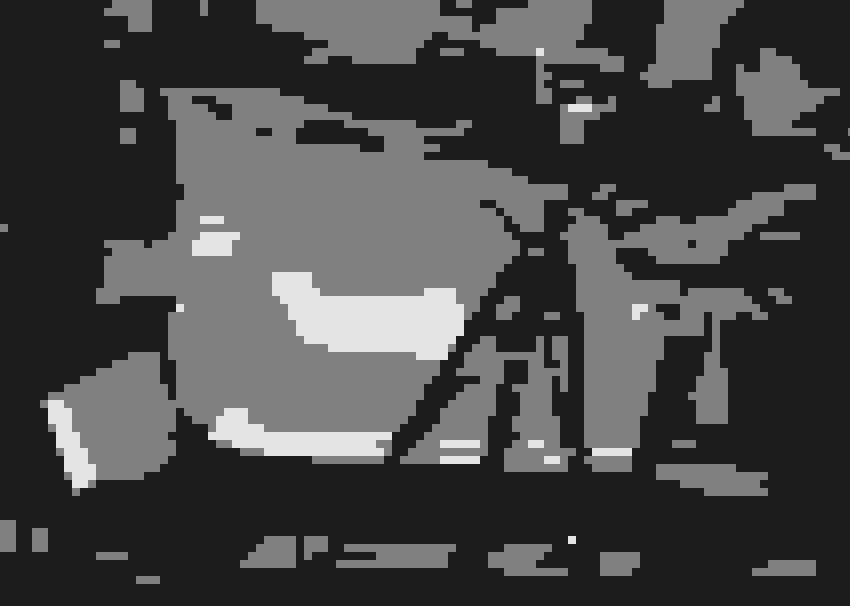
Toyota pickup car site
Holon solutions
Toyota Motor Company needs to open mold to mass produce 2*2m pickup cars. After learning that the three-dimensional scanner can obtain three-dimensional data, through understanding the cooperation with a reading company, the company spent nearly 11 hours scanning the pickup truck carriage, and the accuracy was 0.7mm. During the scanning of peak carriage, due to insufficient scanning format, instability of 3D scanner and other reasons, the data was spliced repeatedly, resulting in data deformation and splicing failure.
1. Preliminary preparation
Spraying developer: improve the surface background color contrast of the sample to obtain better scanning data.
Paste mark points: make the acquired data be positioned and spliced in the scanning software.
2. 3D scanning
Through a friend's introduction, I learned that Hualang 3D has developed a large format 3D scanner hl-3dw for automobiles, and entrusted Hualang 3D to scan the pickup truck. After knowing the specific situation, Hualang 3D engineers used a 3D scanner (hl-3dw). The machine has a fast scanning speed and a scanning depth of 1200mm. The whole scanning process is very stable. It took only 2 hours, and the accuracy of the data obtained from the pickup truck reached 0.1mm. The acquired pickup car data is imported into the reverse design software Geomagic studio to convert the pickup car point cloud data into triangular mesh surface data, which is imported into mainstream reverse software such as pro/e and UG for post-processing, so as to speed up the secondary design of car seats, provide reliable parameters to other relevant departments, ensure that the design results fully meet the production requirements, and speed up the production of pickup cars.
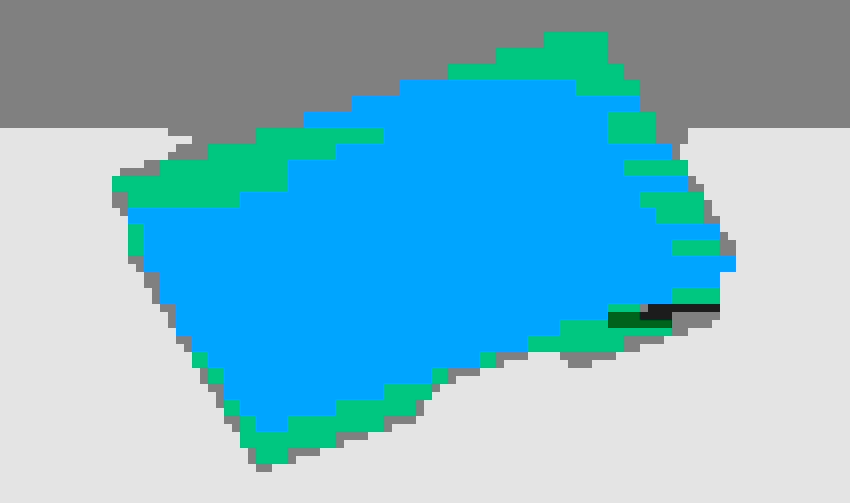
STL data diagram
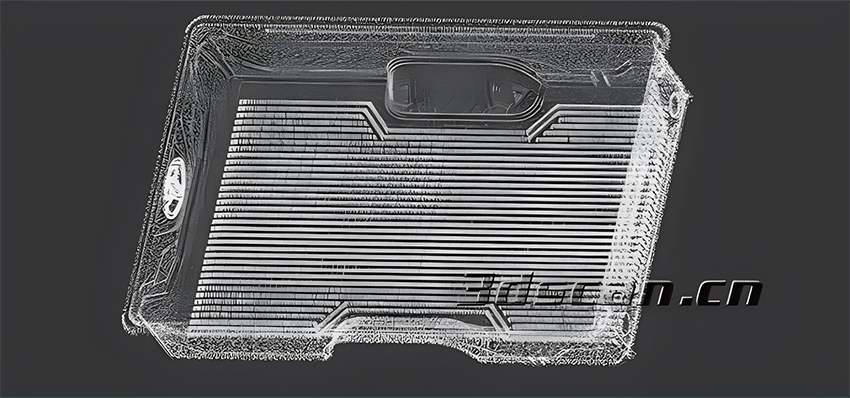
Point cloud data graph