The automobile headlamp shell occupies a large proportion in the automobile spare parts, and its quality will affect the appearance and performance of the automobile. A well-known auto parts manufacturing company needs to obtain the three-dimensional data of the automobile headlamp shell for product structure design and subsequent quality inspection.
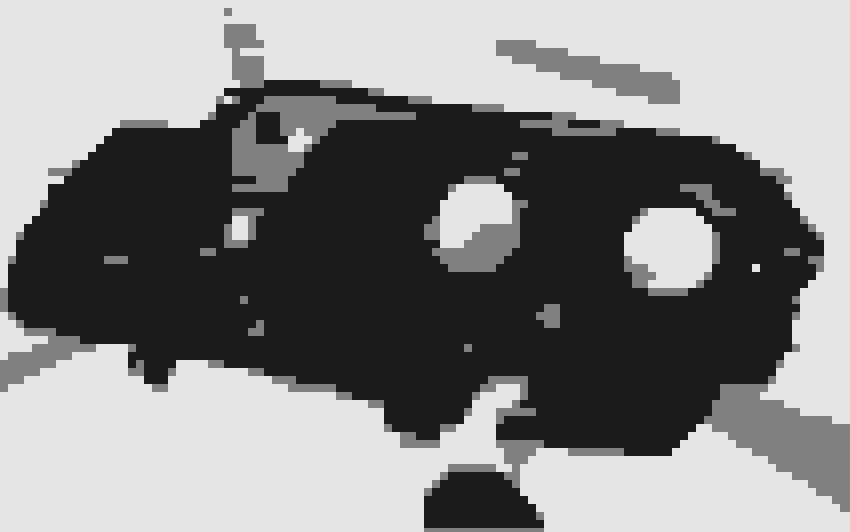
Practical problem
1. The customer requires to quickly obtain the three-dimensional model of the automobile lamp shell. Due to the complex surface and many concave convex surfaces of the lamp shell, it is very difficult to scan.
2. Using the general measurement methods (three coordinates, two-dimensional elements, calipers, etc.), only a small part of the data of the lamp shell can be obtained, and the curved surface part cannot be measured, resulting in the incomplete amount of data obtained, and the secondary design and improvement of the automobile lamp cannot be carried out.
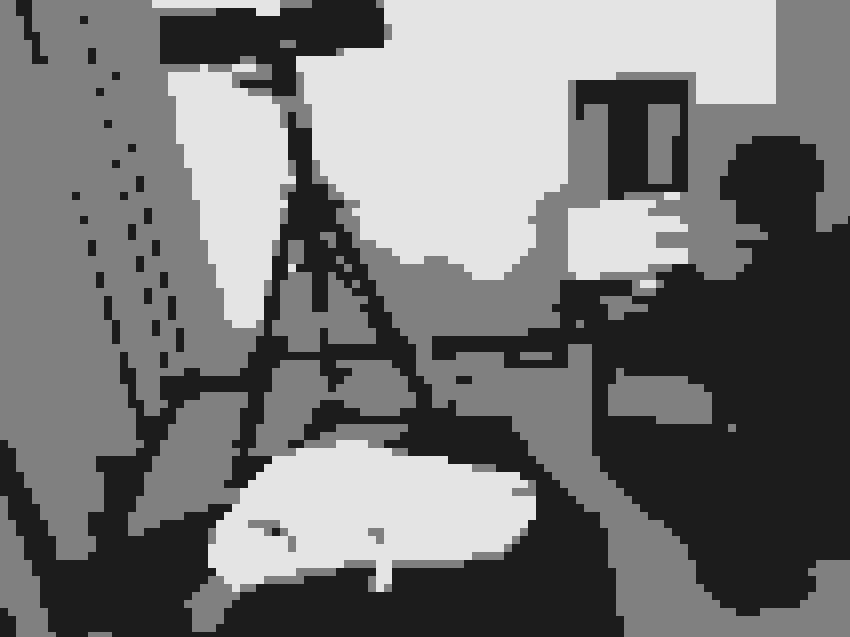
On site scanning of automobile headlamp housing
Holon solutions
The traditional automobile headlamp shell is designed at the same time with the vehicle body to complete the three-dimensional model of the vehicle assembly. Stamping dies are required for car bodies and injection moulds are required for lamps. After different moulds are made, they are tested, assembled and modified. This process requires the cooperation of lamp seats and lamps. That is to say, there are two uncertain factors, which increase the modification cycle and manufacturing cost.
Hualang 3D technical engineers use the industrial 3D scanner hl-3ds+ to quickly scan the automobile headlamp shell to obtain high-density point cloud data. Combined with professional reverse design software, the point cloud data is converted into triangular grid surface data, which is compared with the digital simulation diagram of the automobile headlamp shell, so as to quickly detect the errors and defects of the automobile headlamp shell. Compared with traditional detection methods, Hualang 3D can effectively solve the problems of enterprises and improve their production efficiency.
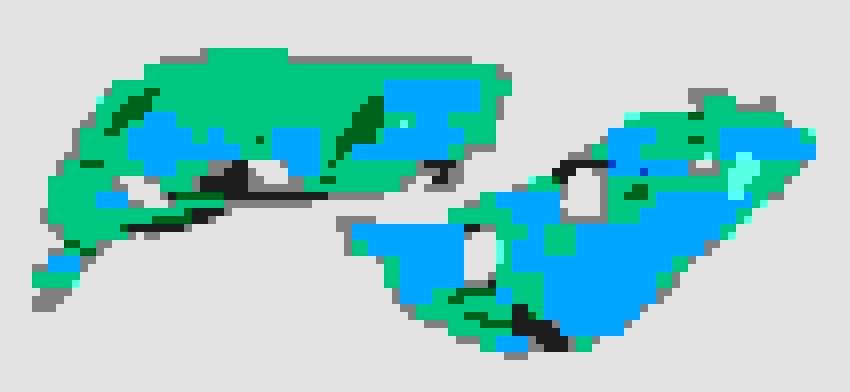
STL data diagram
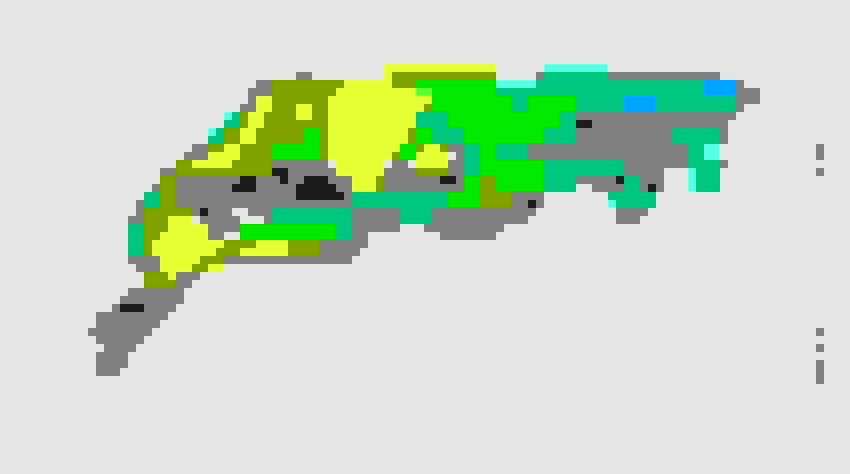
Three dimensional inspection analysis diagram
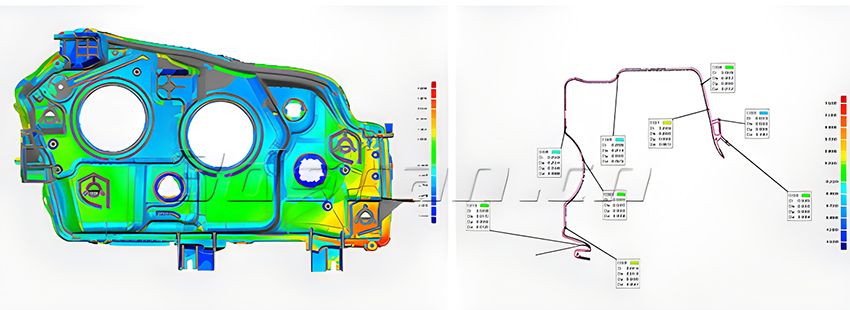
Three dimensional inspection analysis diagram