The frame is a rectangular frame composed of various longitudinal and horizontal steel beams, which is the foundation of the car body. The frame must have sufficient strength and stiffness to withstand the load of the car and the impact from the wheels. The frame structure should meet the general layout of the car, so as to avoid affecting the normal operation of the work during the driving process, and improve the driving stability of the car. It is necessary to understand all aspects of the frame data to better match the design and production, which uses three-dimensional scanning technology to obtain accurate data.
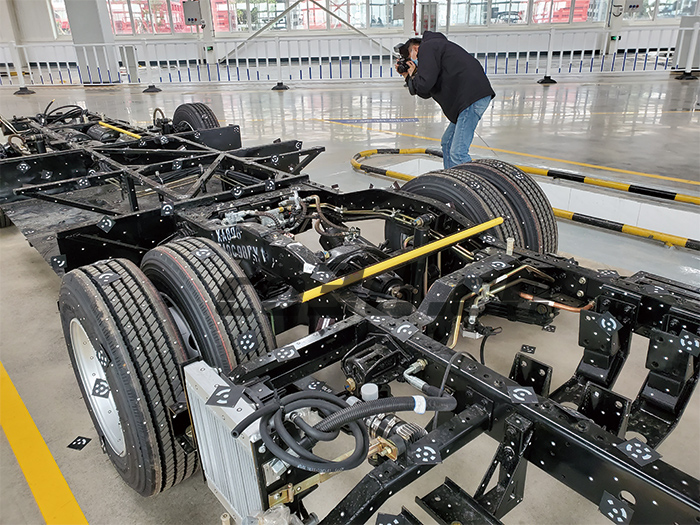
On-site scan of car frame
Practical problems
The overall vehicle underframe is bulky and heavy, which is not conducive to movement. The structure of the external parts is complex, the large and small parts are uneven, and various structural parts are connected, and many details need to be scanned. Brings a certain degree of challenge and difficulty to the scanning work.
If you continue to use the traditional methods in the past, it will take a long time, work efficiency is low, data acquisition is difficult, data accuracy is not high, data cannot be used, and accurate solutions cannot be provided.
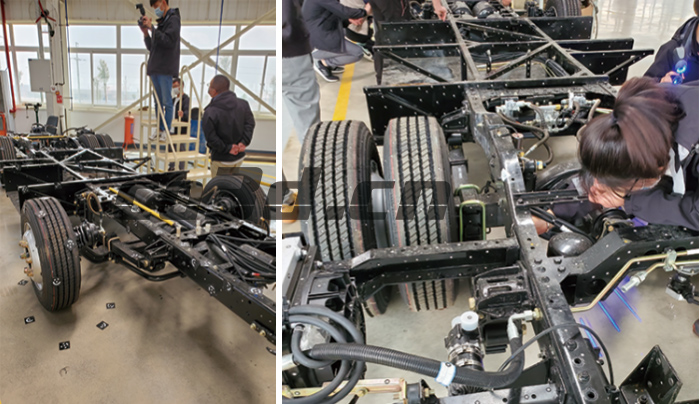
On-site scan of car frame
Holon solutions
According to our company's many years of experience, scanning large workpieces, using our company's 3D photogrammetry system HL-3DP with 3D scanner for scanning measurement. First, mark and code points are pasted on the scanned frame, and then use the three-dimensional photogrammetry system to shoot images of different angles of the underframe, and import the captured images into the HOLON3DP software. Through the triangulation method, the HOLON3DP software automatically combines the images. After the calculation, the 3D coordinate value of the key information on the surface of the object can be obtained. It can correct large-area surface point cloud information and improve the accuracy of the overall point cloud splicing of the 3D scanner. Import the 3D coordinates of the frame into the 3D scanning system, use the handheld 3D scanner A22 to scan the frame quickly and comprehensively, scan the frame from different positions, and use the scanner's fine mode in small places to analyze local features Can be scanned clearly. Moreover, the scanner is visualized when it is in use, and you can see what you are performing in real time, which is convenient and simple to operate.
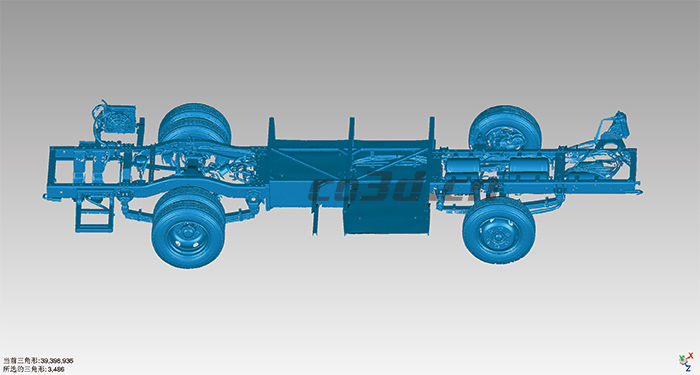
STL data map of car frame
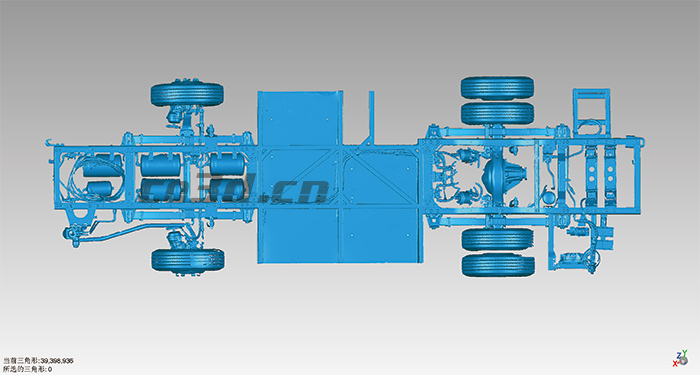
STL data map of car frame
Obtain 3D data and import it into 3D reverse software, perform data reverse modeling, and generate required data reports according to customer requirements. The three-dimensional photogrammetric system HL-3DP is used with a three-dimensional scanner to reduce the cumulative error of three-dimensional scanning data splicing, improve data accuracy, and speed up work efficiency when three-dimensional scanning of super-large workpieces. Solve the customer's problems, provide accurate data solutions, can be used in the follow-up work plan.

STL data map of car frame