The design of the blades in a wind turbine directly affects the conversion efficiency of wind energy, and directly affects its annual power generation. Design airfoils and blades with better aerodynamic performance and conduct aerodynamic analysis. As the aerodynamic shape of the blade, the airfoil directly affects the utilization rate of wind energy by the blade. The advantage of the airfoil is that it has a higher lift coefficient and lift-to-drag ratio under design conditions, and has a good stall performance under non-design conditions.
Practical problems
1. In order to test wind blade products, the company cannot effectively measure wind blades using traditional measurement tools.
2. The surface shape of the wind blade has a large curvature, and ordinary 3D scanner equipment cannot perform accurate 3D data measurement at all.
Holon solutions
A domestic Canadian company tested and certified wind blade products with a length of about 10m and a width of more than 1m. It needed to scan the three-dimensional data of the wind blade and the original two-dimensional map for detection and comparison analysis, and conduct the secondary design and product of the wind turbine blade. Improve work.
In view of the large area of wind turbine blades and many curved surfaces, Hualang 3D engineers proposed the use of scanning equipment in the solution: 3D scanner α7000; 3D photogrammetric system HL-3DP
A. Hualang 3D engineers use the 3D photogrammetry system HL-3DP to take pictures of the tested blades from different angles, and then import the captured pictures into the photogrammetry software, and the software will automatically calculate the whole of the tested blades according to the principle of triangulation. Frame point.
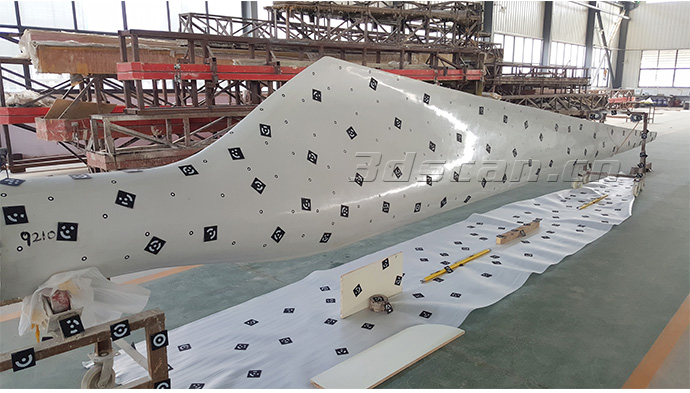
Photogrammetric site for wind turbine blades with a length of about 9m and a width of 1m
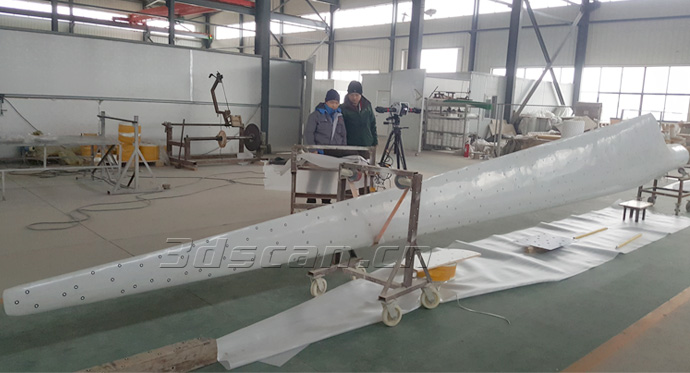
3D scanning site of wind turbine blades
B. The three-dimensional scanner α7000 performs a comprehensive three-dimensional measurement of the wind blade, and obtains the three-dimensional measurement data of the wind turbine blade.
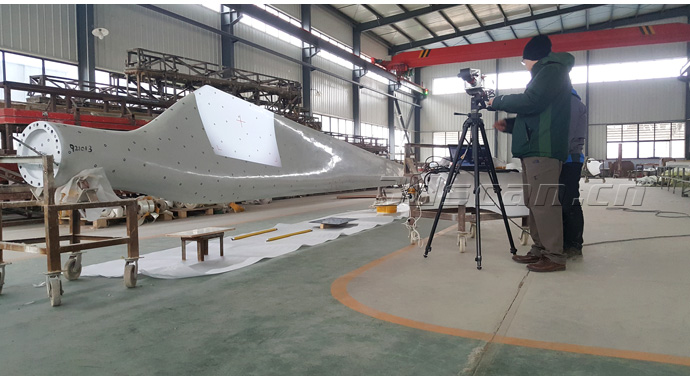
C. Use the reverse design software to analyze the deviation of the digital model size of the high-quality surface model, and then make design adjustments according to the analysis results.
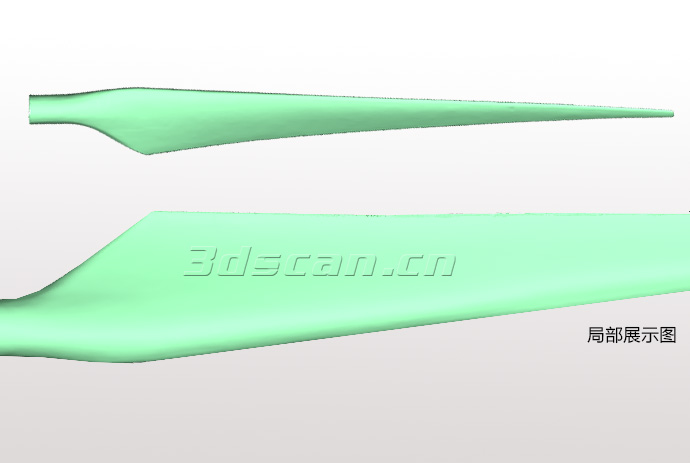
Scanning point cloud data map of wind turbine blades
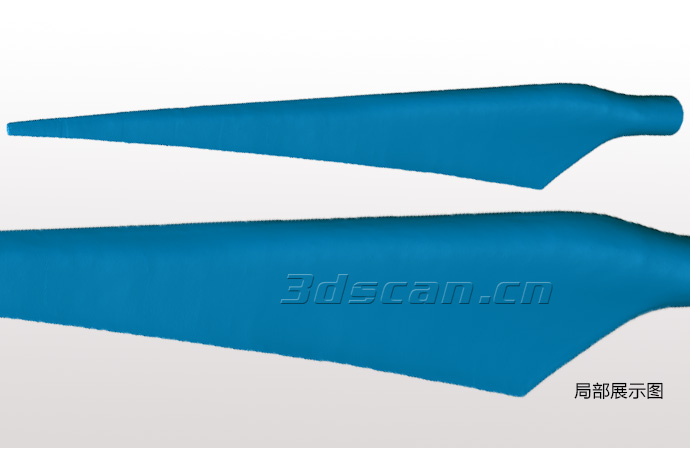
Scanning STL data map of wind turbine blades
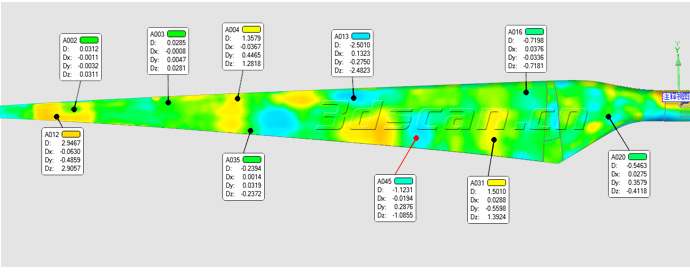
3D detection chromatogram of the left side of the wind blade
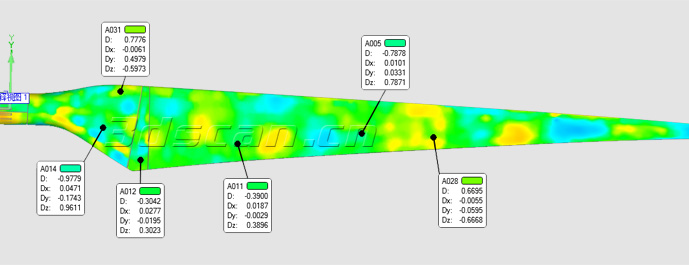
3D detection chromatogram of the right side of the wind blade