With years of operation and development of high-speed rail, a large amount of historical data related to vehicle use has been accumulated. It is necessary to dig out the knowledge behind the data to obtain the law of tread surface wear and dimensional parameter values and the law of vehicle operation stability, and evaluate or predict vehicles and routes. The matching status of the vehicle department is used to guide the wheelset of the vehicle department to be used for maintenance work.
Practical problems
1. The moving wheels are tested with traditional calipers and gauges. Many size and shape features cannot be effectively tested, which greatly affects the detection efficiency and accuracy of the product.
2. The customer needs to quickly scan the outline size of the wheel pair, the inner distance of the wheel pair, the wheel diameter and other parts for dense point cloud collection requirements.
Holon solutions
In the detection of the driving wheel set, due to its huge volume and cumbersome surface, there are many features on the surface and complex three-dimensional free-form surfaces. Traditional calipers and gauges are used for detection. Many size and shape features cannot be effectively detected and prone to secondary Errors greatly affect the detection efficiency and accuracy of the product. In order to abandon traditional inspection methods, "CRRC" needs to use optical three-dimensional inspection equipment to conduct product inspection and secondary design on the production of moving wheel pairs. Hualang technical engineers put forward a solution: use Hualang large-format 3D scanner α7000 to conduct wheel-set 3D inspection and analysis, and obtain a comprehensive analysis and inspection report, which provides effective solutions for the "China CRRC Group" moving wheel-set inspection.
Customer Service: CRRC
Scanning equipment: 3D scanner α7000
Features:
1. The use of carbon fiber military materials: high stability, strong thermal shock resistance, low thermal deformation coefficient, higher scanning accuracy of the equipment, and stronger stability
2. 13-step coding calibration technology: eliminate lens error
3. Multi-frequency phase shift of extrapolation method: uniform fringe projection
4. Compatible with photogrammetry system: higher accuracy
5. Granite calibration source
6. Patented design: eliminates the problem of not being able to stitch in multi-angle scanning
7. The cumulative scanning accuracy is extremely high, and a single machine can scan a workpiece of about 4m
8. Multi-mode scanning, easy to adjust
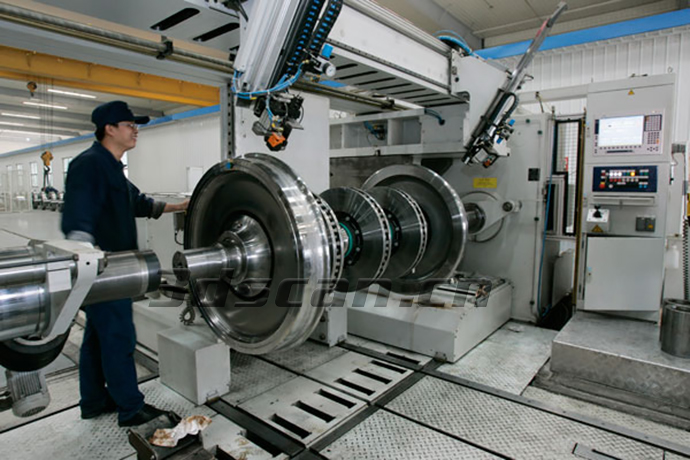
Physical map of driving wheel pair
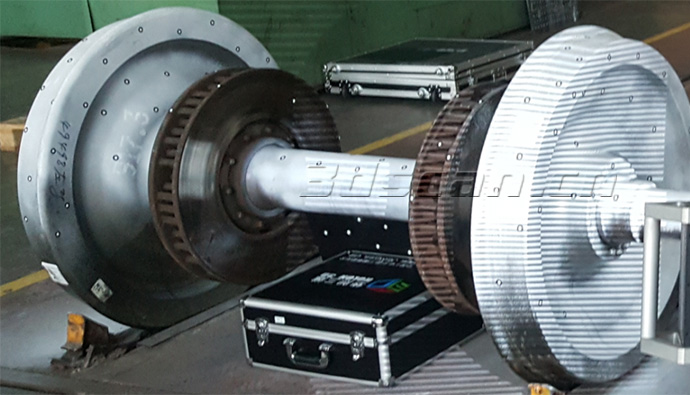
On-site scanning of wheelsets
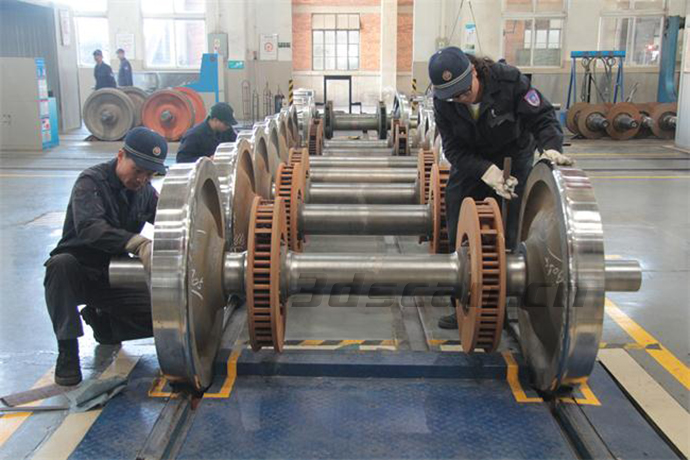
Scanning scene of the driving wheel set
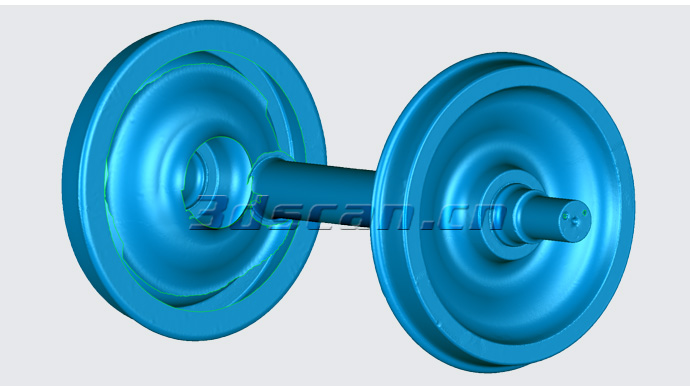
Scanning STL data map of driving wheel pair
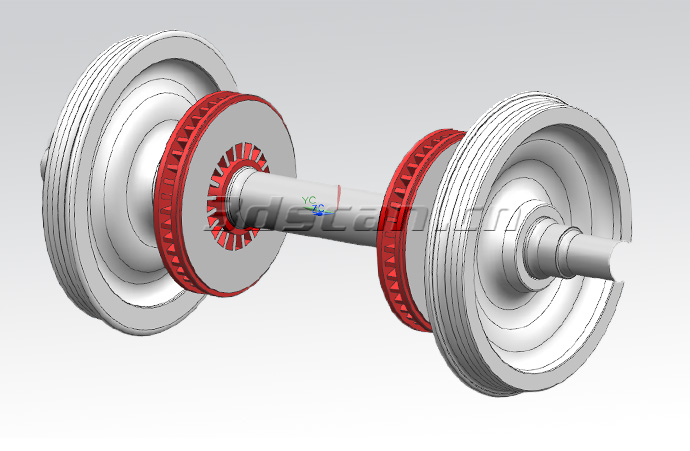
Original digital model diagram of driving wheel pair
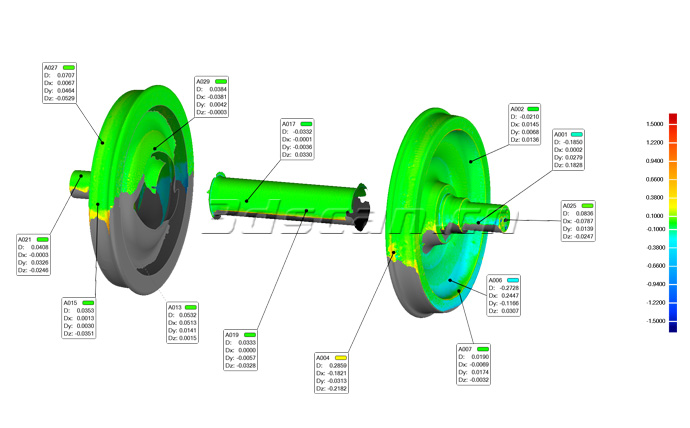
Comparison of original digital model and 3D scanning data to detect chromatogram
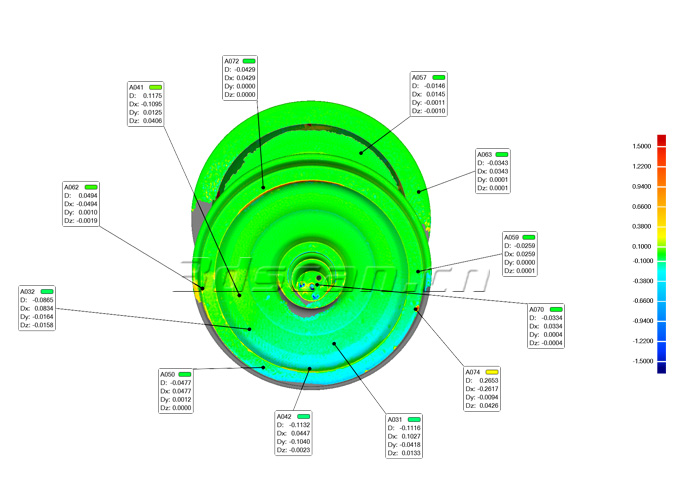
Comparison of original digital model and 3D scanning data to detect chromatogram
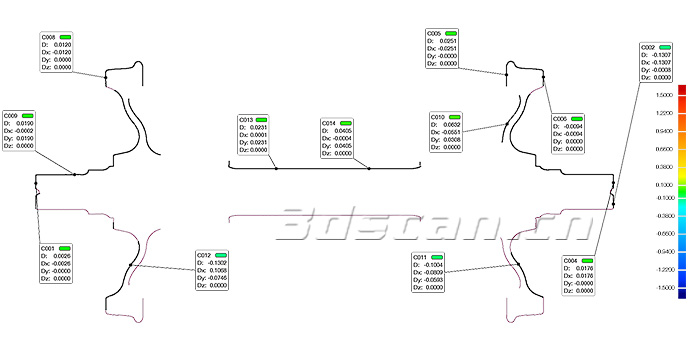
2D cross-sectional dimension drawing of the driving wheel set
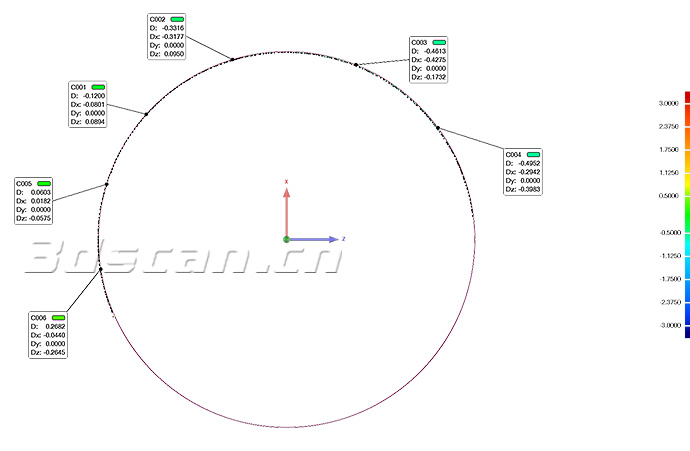
2D cross-sectional dimension drawing of the driving wheel set