During the operation of the steam turbine, the leakage of the steam turbine and the deformation of the cylinder are the most common equipment problems. The tightness of the cylinder joint surface directly affects the safe and economical operation of the unit. Overhaul and scrape the joint surface of the cylinder to make it tight. Important work, in the process of dealing with the steam leakage of the joint surface, it is necessary to carefully analyze the cause of the formation. According to the degree of deformation and the size of the gap, various methods can be comprehensively used to achieve the strict requirements of the joint surface. The customer found Hualang 3D to scan the steam turbine, and the scanned data was reversely designed and processed.
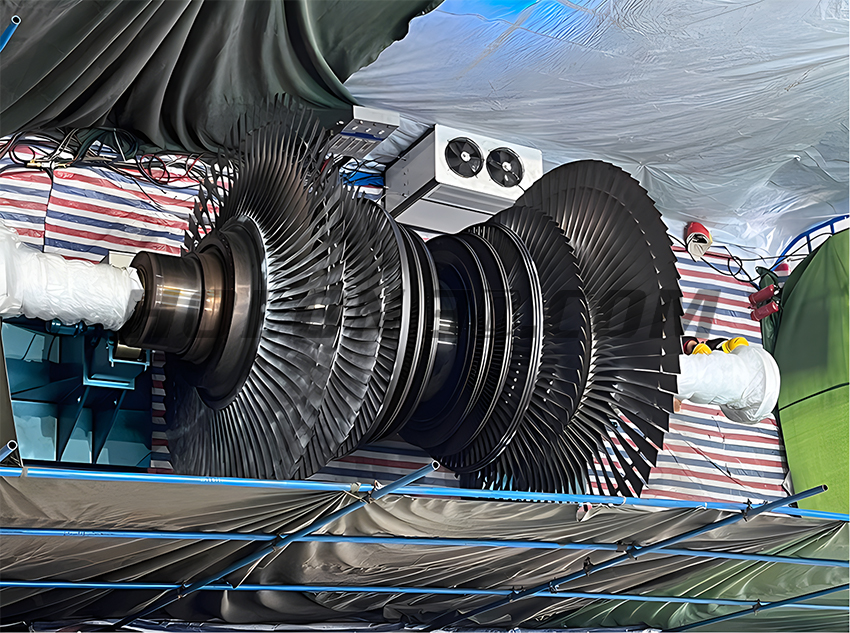
On-site scan of steam turbine
Practical problems
1. The steam turbine has a large volume and a small blade row gap, which is easy to form an included angle, and the customer requires high scanning data accuracy.
2. Customers want to scan 3D data for reverse modeling, which requires fast scanning speed and complete data, which is very challenging.
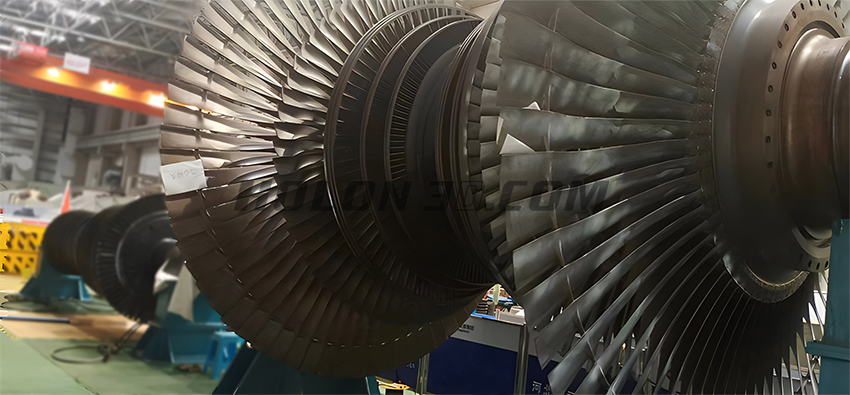
On-site scan of steam turbine
Holon solutions
1. According to the needs of customers, HOLON3D Engineering Division proposed a solution: use the handheld 3D scanner HOLON B71 + 3D photogrammetry HL-3DP to scan the steam turbine. The scanning speed is up to 1,350,000 measurements/second, and the highest accuracy is 0.01mm. The complete 3D data of the steam turbine can be obtained quickly and accurately, providing a reference for the next step of reverse modeling.
2. According to the 3D data of the scanner, HOLON3D engineers used Geomagic Design X reverse design software to model the steam turbine in 3D for later maintenance and reproduction to improve efficiency.
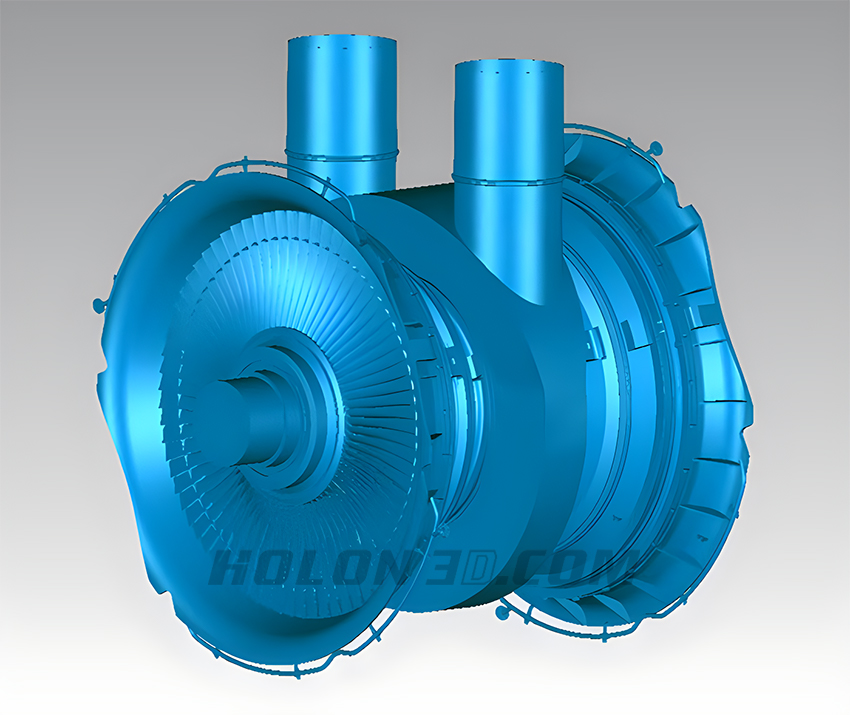
STL data diagram of steam turbine
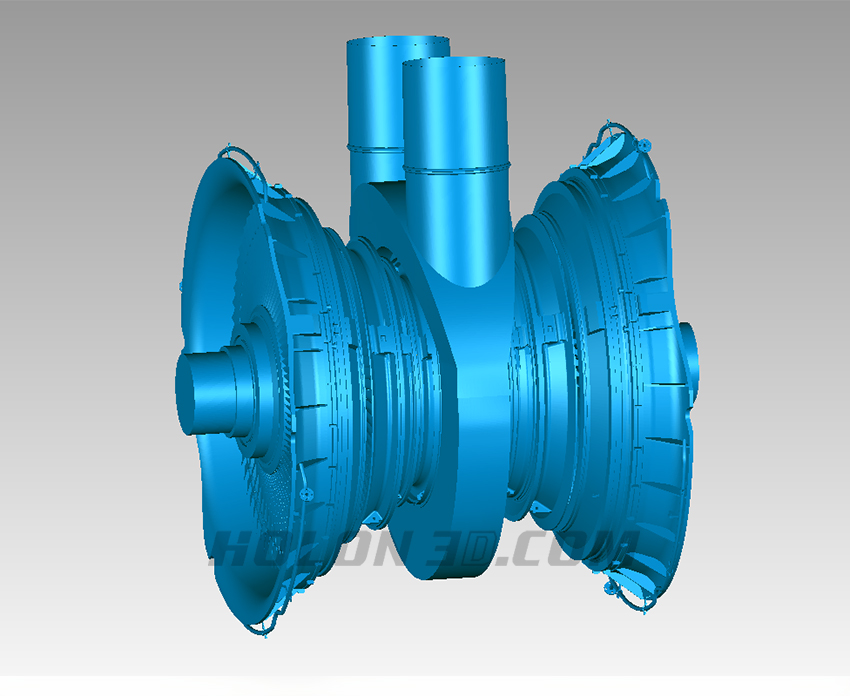
STL data diagram of steam turbine